Ребра жесткости – это конструктивные элементы, предназначенные для повышения прочности и устойчивости различных конструкций к деформациям под воздействием внешних нагрузок․ Их основная функция – увеличение жесткости и сопротивления изгибу, сжатию и кручению․ Правильное применение ребер жесткости позволяет существенно снизить риск разрушения конструкции и продлить срок ее службы․ Они играют важную роль в обеспечении безопасности и надежности различных изделий, от мелких деталей до крупных инженерных сооружений․ Эффективность работы ребер жесткости напрямую зависит от их правильного выбора, учета нагрузки и особенностей конструкции, в которую они интегрируются․ Выбор материала, формы и расположения ребер жесткости – это сложная инженерная задача, требующая точных расчетов и анализа․
Классификация ребер жесткости по материалу
Выбор материала для ребер жесткости определяется множеством факторов, включая требуемую прочность, жесткость, вес конструкции, условия эксплуатации и, конечно же, экономическую целесообразность․ Разнообразие материалов, используемых для производства ребер жесткости, достаточно велико, и каждый из них обладает своими уникальными свойствами и характеристиками․
Металлические ребра жесткости, пожалуй, наиболее распространенный вариант․ Сталь, благодаря своей высокой прочности и доступности, является наиболее популярным материалом․ Различные марки стали, от низкоуглеродистых до высокопрочных легированных, позволяют подобрать оптимальный вариант для конкретных условий эксплуатации․ Алюминиевые сплавы, несмотря на меньшую прочность по сравнению со сталью, часто используются в случаях, когда важен низкий вес конструкции, например, в авиационной и космической промышленности․ Титановые сплавы, характеризующиеся высокой прочностью и коррозионной стойкостью, применяются в особо ответственных конструкциях, где требуется максимальная надежность․
Полимерные ребра жесткости становятся все более востребованными благодаря своим преимуществам, таким как низкая стоимость, легкость обработки и возможность создания сложных форм․ Полипропилен, полиэтилен, полиамид и другие полимеры широко используются в производстве ребер жесткости для различных применений, особенно в тех случаях, где не требуется высокая прочность․ Композитные материалы, сочетающие в себе свойства полимеров и армирующих волокон (стекловолокно, углеволокно), позволяют создавать ребра жесткости с высокой прочностью и жесткостью при относительно небольшом весе․ Этот тип ребер жесткости находит применение в автомобилестроении, судостроении и других отраслях, где важна оптимизация веса конструкции․
Деревянные ребра жесткости, традиционный материал, используются в основном в строительстве и мебельной промышленности․ Их преимущество – экологичность и доступность․ Однако, дерево менее прочно и устойчиво к воздействию влаги и насекомых по сравнению с металлами и полимерами․ Поэтому применение деревянных ребер жесткости ограничено конструкциями, работающими в благоприятных условиях․
Выбор материала для ребер жесткости – это компромисс между требуемыми характеристиками прочности, жесткости, веса, стоимости и условиями эксплуатации․ Инженеры тщательно анализируют все эти факторы, чтобы выбрать оптимальный материал, обеспечивающий надежность и долговечность конструкции․
Кроме того, важно учитывать технологичность обработки выбранного материала․ Например, металлические ребра жесткости могут быть изготовлены методом штамповки, сварки, литья, а полимерные – литьем под давлением, экструзией или формованием․ Выбор метода производства также влияет на конечную стоимость и качество изделия․
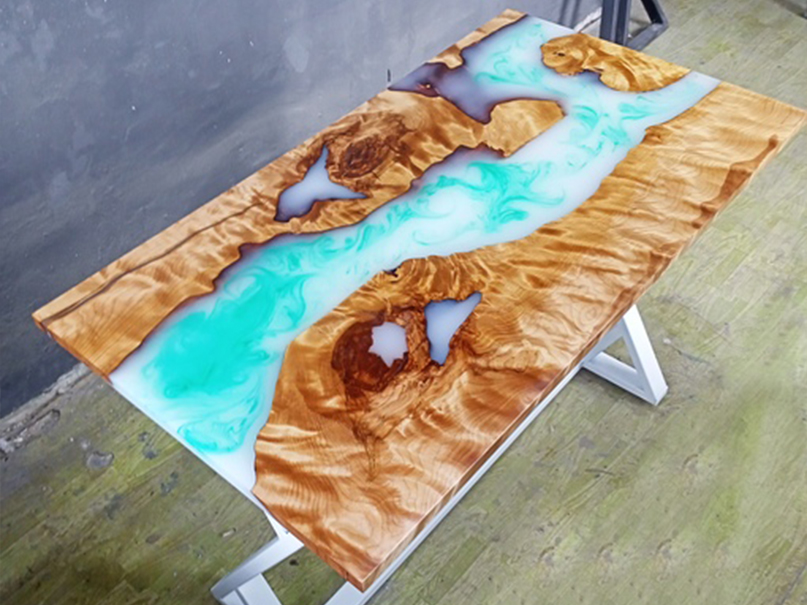
Стол из берёзового слэба и эпоксидной смолы
31 200 ₽
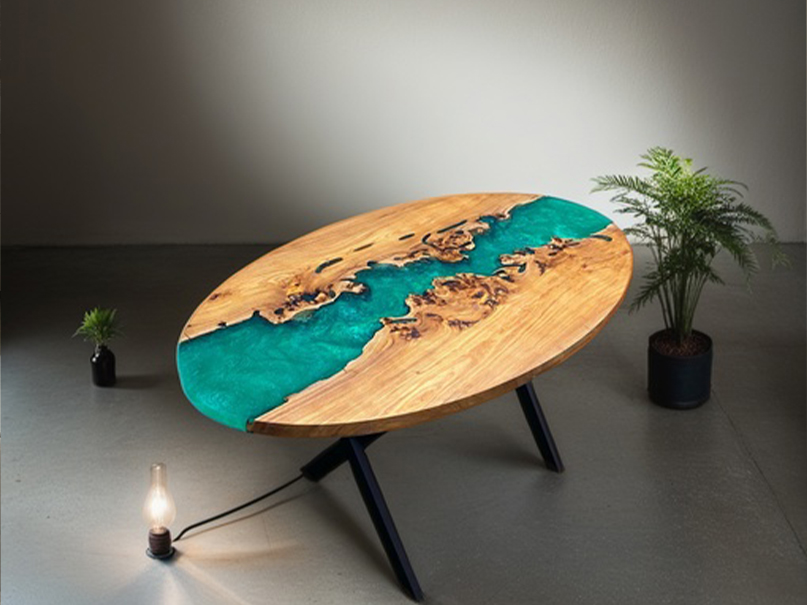
Овальный стол из эпоксидной смолы
69 000 ₽
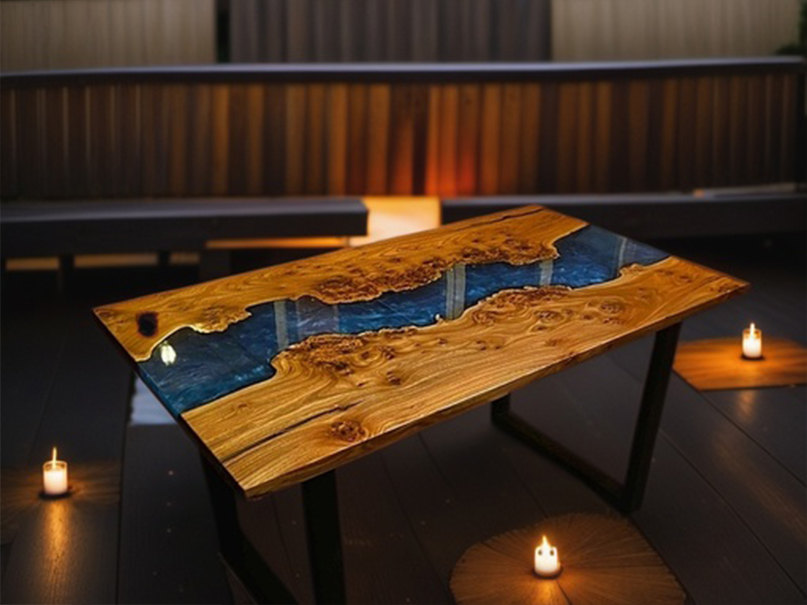
Стол из Карагача и эпоксидной смолы
63 000 ₽
Виды ребер жесткости по форме и конструкции
Разнообразие форм и конструкций ребер жесткости обусловлено широким спектром задач, которые они призваны решать․ Выбор оптимальной формы и конструкции напрямую зависит от типа нагрузок, геометрии укрепляемой конструкции и требований к ее прочности, жесткости и весу․ Неправильный выбор может привести к снижению эффективности ребер жесткости или даже к повреждению конструкции․
По форме ребра жесткости могут быть самыми разнообразными⁚ прямоугольными, треугольными, трапециевидными, L-образными, U-образными, Z-образными и многими другими․ Выбор формы определяется расположением ребра жесткости относительно нагружаемой поверхности и характером действующих сил․ Например, для повышения сопротивления изгибу часто используются ребра прямоугольной или Т-образной формы, а для увеличения устойчивости к сжатию – ребра треугольной или трапециевидной формы․
По конструкции ребра жесткости могут быть сплошными или перфорированными․ Сплошные ребра жесткости обеспечивают максимальную прочность и жесткость, но при этом имеют больший вес․ Перфорированные ребра жесткости, имеющие отверстия различной формы и размера, позволяют снизить вес конструкции без существенного уменьшения прочности․ Выбор между сплошными и перфорированными ребрами жесткости определяется компромиссом между прочностью, весом и стоимостью․
В зависимости от способа соединения с основной конструкцией различают ребра жесткости, прикрепленные сваркой, клеем, болтами или заклепками․ Выбор метода соединения определяется материалом ребра жесткости и основной конструкции, а также требованиями к прочности и надежности соединения․ Сварка обеспечивает высокую прочность соединения, но может привести к деформации конструкции․ Клеевое соединение позволяет избежать деформации, но менее прочно, чем сварное․ Болтовое и заклепочное соединения являются разъемными и позволяют легко демонтировать ребра жесткости․
Также существуют комбинированные конструкции ребер жесткости, сочетающие в себе различные формы и материалы․ Например, ребро жесткости может состоять из металлического каркаса и заполненного полимерным материалом․ Такие конструкции позволяют оптимизировать прочность, жесткость и вес конструкции․
Особый тип ребер жесткости представляют собой гофрированные профили, обладающие высокой прочностью и жесткостью при относительно небольшом весе․ Они часто используются в автомобилестроении, авиационной и строительной промышленности․ Геометрия гофров позволяет эффективно распределять нагрузки и повышать устойчивость конструкции к деформациям․
Выбор формы и конструкции ребер жесткости является сложной инженерной задачей, требующей учета множества факторов и проведения специальных расчетов․ Использование современных методов компьютерного моделирования позволяет оптимизировать дизайн ребер жесткости и обеспечить максимальную эффективность их работы․
Области применения ребер жесткости в различных отраслях
Ребра жесткости – это универсальные конструктивные элементы, нашедшие широкое применение в самых разных отраслях промышленности и строительства․ Их использование обусловлено необходимостью повышения прочности, жесткости и устойчивости различных конструкций к различным видам нагрузок․ Благодаря разнообразию материалов, форм и способов изготовления, ребра жесткости позволяют решать самые сложные инженерные задачи․
В автомобилестроении ребра жесткости используются повсеместно⁚ в кузовах автомобилей, для усиления элементов подвески, в рамных конструкциях․ Они повышают жесткость кузова, улучшают безопасность пассажиров при столкновениях, и снижают уровень вибраций․ Часто используются штампованные стальные ребра жесткости, а также композитные материалы для снижения веса автомобиля․
В авиационной и космической промышленности ребра жесткости играют критически важную роль․ Они используются в конструкции самолетов, вертолетов, ракет и спутников․ Здесь особое внимание уделяется снижению веса конструкции при одновременном обеспечении высокой прочности и жесткости․ В этих отраслях широко применяются легкие и прочные материалы, такие как алюминиевые и титановые сплавы, а также композитные материалы на основе углеродного волокна․
В строительстве ребра жесткости используются для усиления стен, перекрытий, фундаментов и других конструктивных элементов зданий и сооружений․ Они повышают сейсмостойкость зданий, улучшают их устойчивость к ветровым нагрузкам и предотвращают прогибы․ Здесь часто применяются металлические и железобетонные ребра жесткости․
В судостроении ребра жесткости используются для усиления корпуса судов, обеспечения их прочности и непроницаемости․ Они также применяются в конструкции палуб и переборок․ В этой отрасли важно обеспечить коррозионную стойкость ребер жесткости, поэтому часто используются нержавеющие стали и другие коррозионно-стойкие материалы․
В производстве мебели ребра жесткости используются для повышения прочности и жесткости каркасов столов, стульев, шкафов и другой мебели․ Они позволяют создавать более надежные и долговечные изделия․ Здесь часто используются деревянные и металлические ребра жесткости․
В производстве бытовой техники ребра жесткости применяются для усиления корпусов холодильников, стиральных машин, микроволновых печей и другой бытовой техники․ Они повышают жесткость корпуса и предотвращают его деформацию при транспортировке и эксплуатации;
Это лишь некоторые примеры применения ребер жесткости․ Их использование постоянно расширяется с развитием новых материалов и технологий․ Благодаря своей универсальности и эффективности, ребра жесткости являются неотъемлемой частью многих инженерных конструкций․
Развитие технологий и постоянно растущие требования к прочности, легкости и долговечности конструкций стимулируют постоянное совершенствование методов производства и использования ребер жесткости․ Современные тенденции направлены на создание более эффективных, легких и экономичных решений в этой области․
Перспективным направлением является использование новых материалов, обладающих уникальными свойствами․ Композитные материалы, такие как углеродные и арамидные волокна, позволяют создавать ребра жесткости с высокой прочностью и жесткостью при минимальном весе․ Исследования в области нанотехнологий открывают возможности для создания материалов с еще более улучшенными характеристиками․ Разработка новых полимерных материалов с повышенной прочностью и устойчивостью к воздействию внешней среды также является важным направлением развития․
Важным аспектом является совершенствование технологий производства․ Применение аддитивных технологий (3D-печать) позволяет создавать ребра жесткости сложной формы с высокой точностью и минимальными отходами материала․ Это особенно актуально для изготовления ребер жесткости нестандартных размеров и форм․ Автоматизация производственных процессов позволяет повысить производительность и снизить стоимость изготовления․
Развитие методов компьютерного моделирования позволяет оптимизировать дизайн ребер жесткости, учитывая все необходимые параметры и нагрузки․ Это позволяет создавать более эффективные и надежные конструкции с минимальным расходом материала․ Применение методов элементного конечного элемента (МКЭ) позволяет точно рассчитать напряжения и деформации в конструкции и оптимизировать геометрию ребер жесткости для достижения максимальной прочности и жесткости․
Не менее важна разработка новых методов соединения ребер жесткости с основной конструкцией․ Постоянно совершенствуются технологии сварки, клееных и болтовых соединений, что позволяет повысить надежность и прочность соединений и снизить вероятность их разрушения․ Исследования в области новых клеев и герметиков позволяют создавать более прочные и долговечные клеевые соединения․
В целом, перспективы развития производства ребер жесткости связаны с использованием новых материалов, совершенствованием технологий производства и расширением областей применения․ Развитие компьютерного моделирования и аддитивных технологий играет ключевую роль в создании более эффективных и надежных конструкций, что позволяет создавать более легкие, прочные и долговечные изделия в различных отраслях промышленности․