Выбор исходной эпоксидной смолы
Выбор исходной эпоксидной смолы критически важен для достижения высокой термостойкости конечного продукта. Обратите внимание на марки ЭД-6 и ЭД-15, способные выдерживать температуры до 250°C. Однако, для еще большей термостойкости (более 300°C, как упоминается в некоторых источниках), необходимо искать специализированные смолы, например, LG800 (с термостойкостью 220-280°C), или смолы на основе фторированных дифенилолпропанов. Важно учитывать, что термостойкость зависит от химического строения смолы и процесса отверждения. Не стоит забывать о рекомендованных температурных режимах эксплуатации, которые могут варьироватся от -50°C до 150°C, в зависимости от конкретного типа смолы.
Влияние химического строения на термостойкость
Химическое строение эпоксидной смолы является определяющим фактором ее термостойкости. Как указывалось в различных источниках, количество эпоксидных групп в молекуле напрямую влияет на конечные свойства материала. Чем больше эпоксидных групп (меньше эпоксидно-диановое число, например, в смолах ЭД-8 и ЭД-16), тем выше потенциальная термостойкость отвержденной смолы. Это связано с тем, что более плотная сшивка молекулярных цепей, достигаемая за счет большего числа реакционноспособных групп, приводит к более жесткой и термостойкой структуре полимера. Однако, нужно понимать, что простое увеличение количества эпоксидных групп не всегда гарантирует значительное повышение термостойкости. Другие структурные особенности, такие как тип и расположение заместителей в молекуле эпоксидной смолы, также играют важную роль. Например, введение ароматических колец или фторсодержащих групп может существенно повысить термостойкость, как это наблюдается в специализированных высокотемпературных эпоксидных смолах. Ароматические полиамины, используемые в качестве отвердителей, также влияют на повышение прочности и термостойкости конечного продукта. Важно отметить, что невозможно просто добавить модификаторы к любой эпоксидной смоле для мгновенного повышения ее термостойкости. Нужен комплексный подход, включающий тщательный подбор как исходной смолы, так и отвердителя, с учетом их химического строения и совместимости. Изучение влияния различных химических модификаций на термостойкость требует специализированных знаний и экспериментальных исследований.
Типы эпоксидных смол с повышенной термостойкостью
На рынке представлен широкий спектр эпоксидных смол, отличающихся по своим характеристикам, в т.ч. и по термостойкости. Для достижения высоких температурных показателей необходимо выбирать специальные составы, разработанные для работы в экстремальных условиях. Встречаются упоминания о смолах, способных выдерживать температуры до 300°C и выше, хотя в большинстве случаев указанные значения относятся к кратковременному воздействию. Более распространены смолы с термостойкостью до 250°C, например, марки ЭД-6 и ЭД-15, которые часто используются в приложениях, требующих повышенной жаростойкости. Однако, эти марки не являются единственными вариантами. Существуют и другие специализированные эпоксидные системы, разработанные для конкретных применений. Например, смола LG800, описанная в некоторых источниках, показывает термостойкость в диапазоне 220-280°C. Ее применение предполагает последовательное отверждение по строгому графику, что критически важно для достижения заявленных характеристик. Также упоминаются термостойкие органосиликатные герметизирующие материалы на основе эпоксидных смол. Выбор конкретного типа смолы зависит от требуемых температурных параметров, длительности воздействия высоких температур, а также от других важных эксплуатационных характеристик, таких как прочность, эластичность и химическая стойкость. Важно отметить, что термостойкость не единственный фактор, который следует учитывать при выборе эпоксидной смолы. Необходимо внимательно изучить техническую документацию и условия применения каждого конкретного типа смолы для обеспечения надежности и долговечности готового изделия. Для особо высоких требований к термостойкости, следует рассмотреть смолы на основе фторированных дифенилолпропанов, которые демонстрируют наилучшие показатели в данном отношении. Помимо марки и типа смолы, ключевым фактором остается правильное соблюдение технологии отверждения, что существенно влияет на конечную термостойкость.
Методы повышения термостойкости
Повышение термостойкости эпоксидной смолы возможно за счет использования специальных добавок и наполнителей. Выбор наполнителя зависит от требуемых свойств конечного продукта. Правильный температурный режим отверждения также играет ключевую роль. Некоторые источники указывают на важность последовательного отверждения по графику, например, для смолы LG800. Для достижения максимальной термостойкости необходимо тщательно следовать рекомендациям производителя по подготовке и применению смолы и отвердителя.
Использование специальных добавок и наполнителей
Включение специальных добавок и наполнителей в эпоксидную смолу – эффективный метод повышения ее термостойкости. Выбор подходящих компонентов зависит от желаемых свойств конечного материала и требуемого уровня повышения термостойкости. Некоторые наполнители не только увеличивают термостойкость, но и улучшают другие характеристики, такие как прочность, твердость или химическая стойкость. Например, добавление определенных видов наполнителей может увеличить теплопроводность композита, что поможет быстрее отводить тепло и предотвращать перегрев. Среди распространенных наполнителей можно выделить различные виды минеральных порошков (например, кварцевый песок, алюмосиликаты), керамические микросферы, графит, а также специальные высокотемпературные волокна (например, углеродные или керамические волокна). Каждый из этих наполнителей обладает уникальным набором свойств, и их влияние на термостойкость эпоксидной смолы может быть различным. Кроме наполнителей, могут использоваться и специальные добавки, которые модифицируют химическое строение полимерной матрицы и улучшают ее термостойкость. Это могут быть различные модификаторы, улучшающие сшивку полимера, или добавки, повышающие его тепловую стабильность. Важно помнить, что добавление наполнителей и добавок может изменять другие свойства эпоксидной смолы, такие как вязкость, прочность на сжатие или изгиб, прозрачность. Поэтому необходимо тщательно подбирать состав и соотношение компонентов, исходя из конкретных требований к свойствам готового материала. Для достижения оптимальных результатов рекомендуется проводить испытания и подбирать наполнители и добавки экспериментальным путем. Не всегда большее количество наполнителя приводит к пропорциональному увеличению термостойкости. Часто существует оптимальное соотношение, которое обеспечивает наилучшие свойства композита. Поэтому перед применением того или иного наполнителя необходимо провести испытания и выбрать оптимальную его концентрацию.
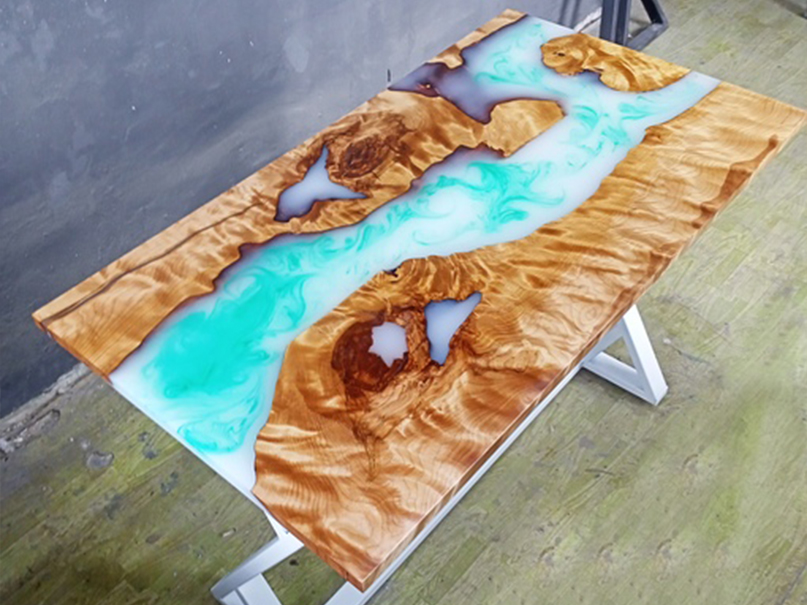
Стол из берёзового слэба и эпоксидной смолы
31 200 ₽
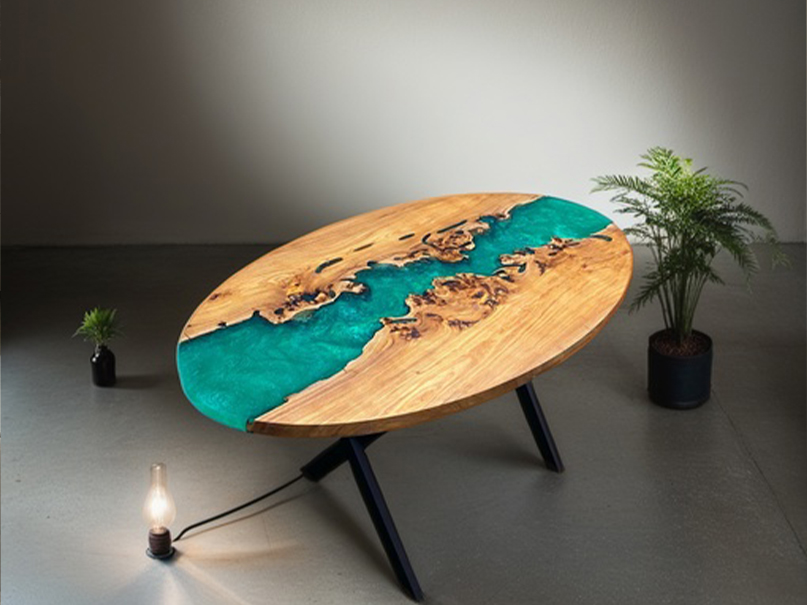
Овальный стол из эпоксидной смолы
69 000 ₽
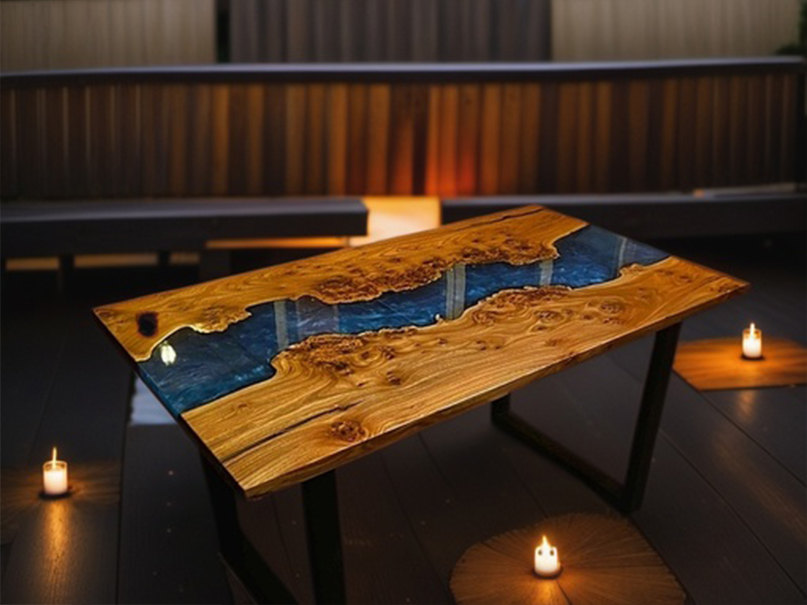
Стол из Карагача и эпоксидной смолы
63 000 ₽
Факторы, влияющие на термостойкость
На термостойкость эпоксидной смолы влияет множество факторов. Ключевым является химический состав исходной смолы и отвердителя, а также их соотношение. Процесс отверждения, включая температурный режим и время выдержки, также критически важен для достижения максимальной термостойкости. Условия окружающей среды во время отверждения, такие как температура и влажность, могут существенно повлиять на конечные свойства материала.
Процесс отверждения и температурный режим
Процесс отверждения эпоксидной смолы – это критически важный этап, определяющий многие свойства конечного материала, включая его термостойкость. Несоблюдение рекомендованных условий отверждения может привести к снижению термостойкости, появлению внутренних напряжений, образованию пор и других дефектов. Температурный режим во время отверждения должен строго соответствовать рекомендациям производителя смолы и отвердителя. Некоторые смолы требуют последовательного повышения температуры по определенному графику, что обеспечивает оптимальную сшивку полимерных цепей и достижение максимальной термостойкости. Например, для смолы LG800 указывается необходимость соблюдения специального графика отверждения. Отклонение от рекомендованного режима может привести к неполному отверждению, образованию слабых мест в структуре материала и значительному снижению его термостойкости. Кроме температуры, на процесс отверждения влияет также время выдержки при той или иной температуре. Слишком короткое время выдержки может не обеспечить полного отверждения, а слишком продолжительное – привести к образованию внутренних напряжений и снижению прочности. Для большинства эпоксидных смол первая стадия отверждения происходит при комнатной температуре (около 24°C), затем может последовательно повышаться температура. Важно также поддерживать стабильность температуры во время отверждения, поскольку колебания могут привести к неравномерности сшивки и снижению термостойкости в отдельных участках изделия. Влажность воздуха также может оказывать влияние на процесс отверждения эпоксидной смолы. Высокая влажность может привести к замедлению или неполному отверждению. Поэтому рекомендуется проводить отверждение в сухих условиях. В целом, оптимизация процесса отверждения, включая температурный режим, время выдержки и контроль влажности, является ключевым фактором для достижения максимальной термостойкости эпоксидных композитов.