Свойства эпоксидной смолы, обеспечивающие защиту от влаги и коррозии
Высокая химическая стойкость эпоксидных смол обусловлена их полимерной структурой, образующей прочную, непроницаемую пленку. Эта пленка эффективно препятствует проникновению воды и агрессивных веществ, вызывающих коррозию. Отсутствие пористости в отвержденном слое – ключевое свойство, обеспечивающее надежную защиту от влаги. Кроме того, эпоксидные смолы обладают отличной адгезией ко многим материалам, что гарантирует прочное сцепление защитного покрытия с поверхностью. Добавление специальных наполнителей может усилить защитные свойства, например, повысить стойкость к ультрафиолетовому излучению или механическим повреждениям. Способность эпоксидных смол образовывать гладкую, бесшовную поверхность также минимизирует возможность попадания влаги и коррозионных агентов под защитный слой. Выбор оптимального типа смолы и отвердителя позволяет настроить свойства покрытия под конкретные условия эксплуатации.
Применение эпоксидной смолы для защиты различных материалов от коррозии
Эпоксидные смолы зарекомендовали себя как универсальное средство защиты от коррозии широкого спектра материалов. Их применение простирается от защиты металлических конструкций в суровых условиях эксплуатации до обработки деталей сложной формы. В машиностроении эпоксидные покрытия защищают детали двигателей, кузова автомобилей, а также различные инструменты и механизмы от воздействия влаги, агрессивных химических сред и механических повреждений, существенно продлевая срок их службы.
В строительной индустрии эпоксидные смолы применяются для защиты металлических каркасов зданий, арматуры, трубопроводов и других конструкций, подверженных коррозии. Они обеспечивают надежную защиту от воздействия атмосферных осадков, грунтовых вод и солей, предотвращая разрушение несущих конструкций. Особо эффективны эпоксидные покрытия в условиях повышенной влажности, например, в бассейнах, ванных комнатах или на судах.
В химической промышленности, где оборудование постоянно контактирует с агрессивными веществами, эпоксидные покрытия незаменимы. Они защищают емкости, трубы, аппаратуру от коррозии, обеспечивая безопасность и надежность технологических процессов. Выбор конкретного типа эпоксидной смолы зависит от химического состава агрессивной среды, температуры эксплуатации и других факторов.
Защита бетонных конструкций также является важной областью применения эпоксидных смолов. Они проникают в поры бетона, укрепляя его структуру и предотвращая проникновение влаги и разрушающих веществ. Это особенно актуально для гидротехнических сооружений, мостов, подземных коммуникаций и других конструкций, эксплуатируемых в условиях повышенной влажности и агрессивных сред. Эпоксидные составы применяються для ремонта поврежденного бетона, восстановления его прочности и водонепроницаемости;
Кроме того, эпоксидные смолы используются для защиты различных металлических изделий бытового назначения⁚ от ограждений и мебели до инструментов и садового инвентаря. Они обеспечивают не только защиту от коррозии, но и придают изделиям эстетичный внешний вид, улучшая их стойкость к царапинам и другим механическим повреждениям. Разнообразие цветовых решений и возможность создания глянцевых или матовых покрытий позволяет адаптировать эпоксидную защиту под любой дизайн. Благодаря своей универсальности и эффективности эпоксидные смолы являются одним из наиболее востребованных материалов для защиты от коррозии в различных отраслях промышленности и быту.
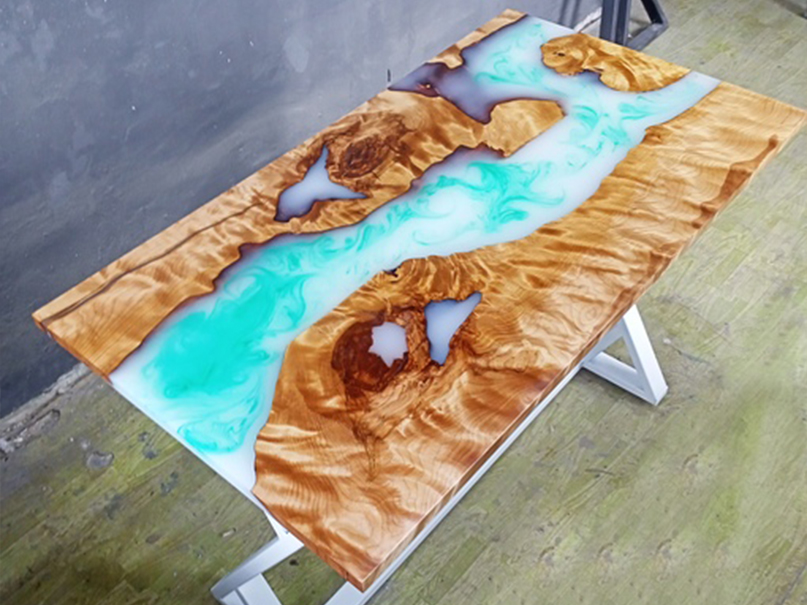
Стол из берёзового слэба и эпоксидной смолы
31 200 ₽
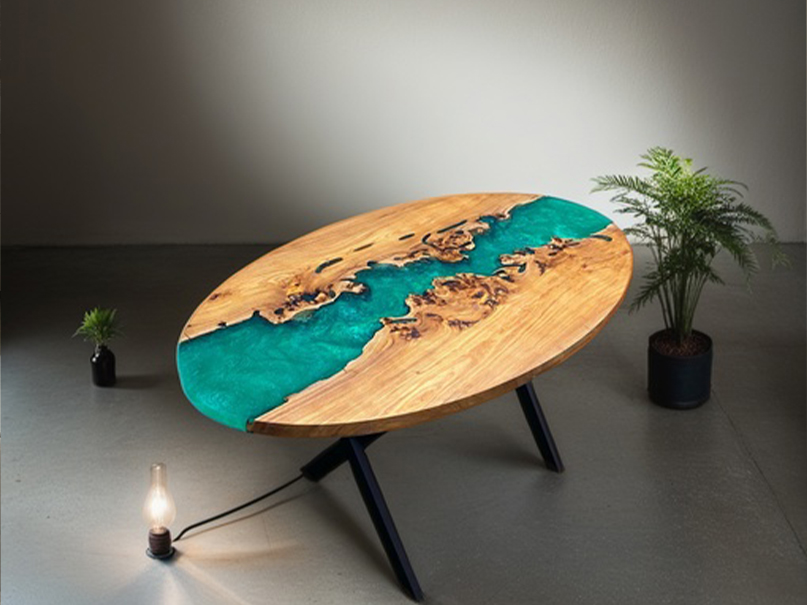
Овальный стол из эпоксидной смолы
69 000 ₽
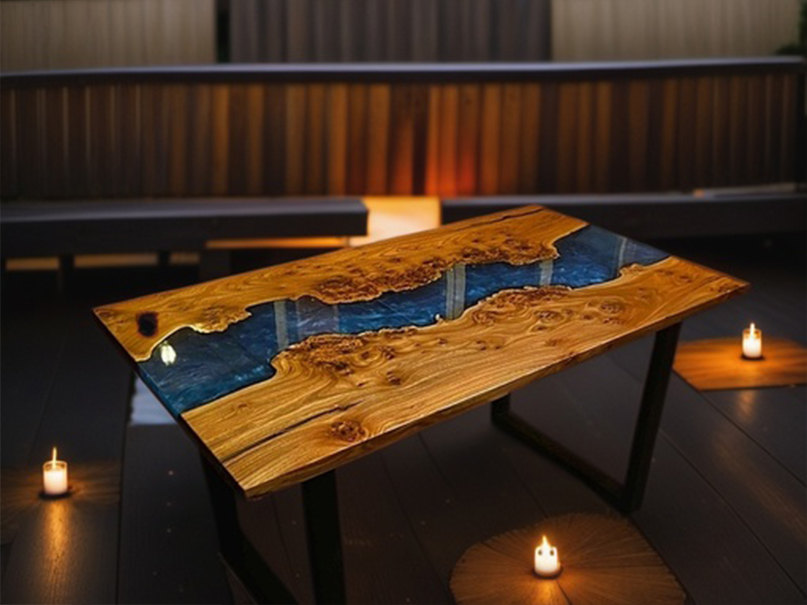
Стол из Карагача и эпоксидной смолы
63 000 ₽
Технология нанесения эпоксидных покрытий⁚ этапы и особенности
Нанесение эпоксидных покрытий – это многоэтапный процесс, требующий соблюдения определенной технологии для достижения максимальной эффективности и долговечности защитного слоя. Качество подготовки поверхности является критическим фактором, определяющим адгезию и долговечность покрытия. Поверхность должна быть тщательно очищена от грязи, пыли, ржавчины, масляных пятен и других загрязнений. Для металлических поверхностей часто используют пескоструйную обработку или шлифование для создания шероховатой поверхности, улучшающей сцепление с эпоксидной смолой. Для бетонных поверхностей может потребоваться дополнительная обработка для удаления рыхлых частиц и повышения прочности основания.
После подготовки поверхности, необходимо тщательно смешать компоненты эпоксидной смолы (смолу и отвердитель) в строгом соответствии с инструкцией производителя. Несоблюдение пропорций может привести к снижению прочности и стойкости покрытия. Смешивание производится обычно с использованием низкоскоростной дрели со специальной насадкой для обеспечения равномерного распределения отвердителя. Важно избегать попадания воздуха в смесь, так как это может привести к образованию пузырьков и снижению качества покрытия.
Нанесение эпоксидного состава может осуществляться различными методами⁚ кистью, валиком, распылением или методом безвоздушного напыления. Выбор метода зависит от площади обрабатываемой поверхности, ее формы и требований к толщине покрытия. Кисть подходит для обработки небольших поверхностей и труднодоступных мест, валик обеспечивает более равномерное нанесение на гладких поверхностях, а распыление – на больших площадях. Безвоздушное напыление позволяет наносить толстые слои покрытия за короткий промежуток времени, что особенно актуально при защите крупных металлических конструкций.
После нанесения эпоксидной смолы необходимо обеспечить оптимальные условия для отверждения. Это включает в себя контроль температуры и влажности окружающей среды. Высокая температура ускоряет процесс отверждения, но может привести к образованию дефектов. Повышенная влажность может замедлить отверждение и снизить качество покрытия. Для больших площадей и сложных конструкций может потребоваться использование специальных камер для контроля климата во время отверждения.
Важно помнить, что нанесение эпоксидных покрытий может потребовать нескольких слоев для достижения необходимой толщины и защиты. Каждый последующий слой наносится после полного отверждения предыдущего. Толщина покрытия определяется исходя из условий эксплуатации и требований к защите от коррозии и влаги. После полного отверждения эпоксидное покрытие образует прочный, долговечный и стойкий к различным воздействиям защитный слой, обеспечивающий надежную защиту от коррозии и влаги для различных материалов и конструкций. Правильное соблюдение технологии нанесения гарантирует максимальную эффективность и долговечность защитного покрытия.
Преимущества и недостатки использования эпоксидной смолы в качестве защитного покрытия
Эпоксидные смолы, как и любой другой материал, обладают своими преимуществами и недостатками при использовании в качестве защитного покрытия от коррозии и влаги. Понимание этих аспектов необходимо для правильного выбора материала и технологии нанесения для конкретных условий эксплуатации. К числу неоспоримых преимуществ эпоксидных покрытий относится их высокая химическая стойкость. Они устойчивы к воздействию многих агрессивных химических веществ, кислот, щелочей и солей, что делает их незаменимыми в химической промышленности и других отраслях, где оборудование подвергается воздействию агрессивных сред. Это свойство позволяет значительно продлить срок службы защищаемых объектов и снизить затраты на ремонт и замену.
Отличная адгезия к различным материалам – еще одно важное преимущество эпоксидных смол. Они хорошо сцепляются с металлами, бетоном, деревом и другими материалами, обеспечивая прочное и надежное покрытие, устойчивое к отслаиванию и растрескиванию. Это особенно важно в условиях вибрации и механических нагрузок, где другие типы покрытий могут быстро разрушаться. Высокая механическая прочность эпоксидных покрытий обеспечивает защиту от истирания, ударов и других механических повреждений, что увеличивает их долговечность и надежность.
Эпоксидные покрытия обладают хорошей водонепроницаемостью, эффективно предотвращая проникновение влаги и предотвращая коррозию. Это свойство особенно важно для защиты металлических конструкций, эксплуатируемых в условиях повышенной влажности, например, в морской среде или в условиях постоянного контакта с водой. Кроме того, эпоксидные смолы позволяют создавать бесшовные покрытия, что минимизирует возможность проникновения влаги и коррозионных агентов под защитный слой. Широкий спектр цветовых решений и возможность создавать покрытия с различными текстурами (глянцевые, матовые) позволяет адаптировать эпоксидную защиту под любой дизайн и требуемые эстетические характеристики.
Однако, несмотря на все преимущества, эпоксидные покрытия имеют и некоторые недостатки. К ним относится относительно высокая стоимость материала и работ по нанесению по сравнению с некоторыми другими типами покрытий. Процесс нанесения эпоксидных покрытий требует соблюдения определенной технологии и наличия специального оборудования, что может усложнить работу и увеличить затраты. Время отверждения эпоксидных смол может быть достаточно длительным, что необходимо учитывать при планировании работ.
Кроме того, эпоксидные смолы чувствительны к низким температурам. При низких температурах процесс отверждения может замедлятся, а прочность покрытия может снижаться. Некоторые типы эпоксидных смол могут быть чувствительны к воздействию ультрафиолетового излучения, что может привести к изменению цвета и снижению прочности покрытия. Поэтому для наружных работ часто применяют эпоксидные смолы со специальными добавками, повышающими стойкость к УФ-излучению. Необходимо учитывать все эти факторы при выборе эпоксидной смолы и технологии ее нанесения для обеспечения максимальной эффективности и долговечности защитного покрытия.
Сравнение эпоксидных покрытий с другими методами защиты от коррозии и влаги
Эпоксидные покрытия являются одним из множества методов защиты от коррозии и влаги, и их эффективность сравнивается с другими популярными технологиями, такими как оцинкование, цинковые или алюминивые краски, и различные виды лакокрасочных материалов. Оцинкование, заключающееся в нанесении цинкового слоя на металлическую поверхность, обеспечивает надежную катодную защиту от коррозии, но менее эффективно в условиях агрессивных химических сред и механических повреждений. По сравнению с оцинковкой, эпоксидные покрытия обладают большей гибкостью в применении, позволяя защищать поверхности сложной формы и детали с узкими зазорами, где нанесение цинкового слоя затруднено. Кроме того, эпоксидные покрытия могут быть окрашены в различные цвета, что важно для эстетических целей.
Цинковые и алюминивые краски обеспечивают более экономичный вариант защиты, чем эпоксидные покрытия, но их стойкость к коррозии и износу, как правило, ниже. Эти краски эффективны при умеренных воздействиях, но в условиях агрессивных сред или при значительных механических нагрузках их защитные свойства могут оказаться недостаточными. Эпоксидные покрытия, в свою очередь, обеспечивают более высокую стойкость к химическим веществам и механическим повреждениям, что делает их предпочтительным вариантом для защиты оборудования в тяжелых условиях эксплуатации.
Сравнение с различными лакокрасочными материалами показывает, что эпоксидные покрытия превосходят многие из них по стойкости к коррозии и химическим воздействиям. Алкидные, акриловые и другие типы красок обеспечивают достаточную защиту в обычных условиях, но в агрессивных средах их стойкость значительно ниже, чем у эпоксидных покрытий. Эпоксидные покрытия также обладают лучшей адгезией к металлам и бетону, что обеспечивает более прочное и долговечное защитное покрытие. Однако, лакокрасочные материалы часто более доступны и просты в нанесении, что делает их выгодным вариантом для некритичных приложений.
Выбор между эпоксидными покрытиями и другими методами защиты от коррозии зависит от конкретных условий эксплуатации. Если требуется высокая стойкость к коррозии и химическим воздействиям, а также прочность и долговечность покрытия, то эпоксидные покрытия являются предпочтительным вариантом. В случаях, где стоимость является основным критерием выбора, и условия эксплуатации не являются чрезмерно агрессивными, более экономичные варианты, такие как цинковые или алюминивые краски, могут быть достаточными. Поэтому правильный выбор метода защиты требует тщательного анализа условий эксплуатации и оценки свойств различных материалов.